Dimensional Parameters of Wave Springs and Their Significance
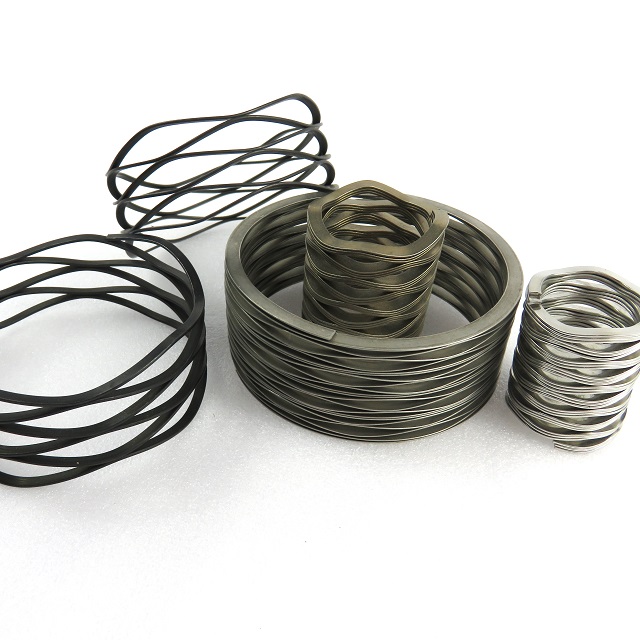
As a critical component in aerospace, automotive manufacturing, precision instruments, and many other fields, the dimensional parameters of wave springs play a fundamental role in determining their performance. A thorough understanding of these parameters is essential for optimizing mechanical design, improving product quality, and driving industry advancement. Today, we will briefly discuss several key dimensional parameters of wave springs:
1. Inner Diameter
The inner diameter, also known as the shaft fitting diameter, refers to the diameter of the internal circular opening of the wave spring. It determines the maximum shaft or rod diameter the spring can fit onto. For example, in a mechanical transmission system, if the shaft diameter is 20 mm, the wave spring’s inner diameter must be slightly larger than 20 mm to ensure smooth installation. A properly sized inner diameter prevents excessive tightness, which could hinder shaft rotation, or excessive looseness, which could reduce the spring’s effectiveness in applications such as damping and clamping.
2. Outer Diameter
The outer diameter, also known as the hole fitting diameter, refers to the diameter of the outermost circular edge of the wave spring. This parameter is closely related to the available installation space. If a wave spring needs to be installed inside a compact enclosure, an excessively large outer diameter may prevent proper placement. Together with the inner diameter, the outer diameter defines the radial dimensions of the spring, affecting its radial elasticity. In applications where a strong elastic force is needed within a limited space, a well-designed outer diameter ensures optimal performance while maintaining compatibility with the installation environment.
3. Wire Width
Wire width refers to the width of the metal strip (or other material) that forms the wave spring. It significantly impacts the strength and elasticity of the spring. A wider strip allows the spring to withstand greater axial or radial loads without deformation. For example, when subjected to high axial loads, a wider strip provides better support. Additionally, wire width influences the fatigue life of the spring—wider strips may offer improved resistance to fatigue failure under repeated loading and unloading conditions.
4. Thickness
Thickness refers to the axial dimension of the wave spring and plays a crucial role in determining its axial elastic force and deformation characteristics. For instance, in applications requiring precise axial displacement control, adjusting the spring’s thickness can help achieve the desired elastic restoring force, ensuring stable operation within a defined displacement range. A thicker wave spring typically generates a greater elastic force under the same compression, making it suitable for applications requiring high axial support.
5. Number of Turns
The number of turns refers to the total number of complete loops in a wave spring. This parameter directly affects the spring’s elastic coefficient. Generally, more turns result in greater elastic deformation under the same compression or tension conditions, leading to a lower spring stiffness. For example, in systems designed to absorb significant impact forces, a wave spring with more turns provides greater deformation capacity, effectively slowing down impact forces and protecting other system components. The number of turns also influences the stability of the spring—an appropriate number of turns helps prevent twisting or instability during operation.
6. Number of Waves
The number of waves refers to the number of wave formations along the circumference of the spring. It determines the complexity of the spring’s shape and the distribution of its elastic force. A higher number of waves allows for a more even distribution of elastic force around the circumference. For example, in applications requiring uniform force distribution in the circumferential direction, such as sealing systems in rotating equipment, an appropriate number of wave sensures consistent sealing pressure and enhances sealing performance. Additionally, modifying the number of waves can influence the overall stiffness of the spring, making it an effective design parameter for applications requiring specific stiffness levels.These key dimensional parameters may seem simple, but they play a decisive role in defining the performance and application of wave springs. Each parameter is interrelated and influences the others, collectively shaping the unique functionality of wave springs in various mechanical systems.
- Art
- Causes
- Crafts
- Dance
- Drinks
- Film
- Fitness
- Food
- Games
- Gardening
- Health
- Home
- Literature
- Music
- Networking
- Other
- Party
- Religion
- Shopping
- Sports
- Theater
- Wellness