Dacromet Coating Process for Spring Surface Treatment
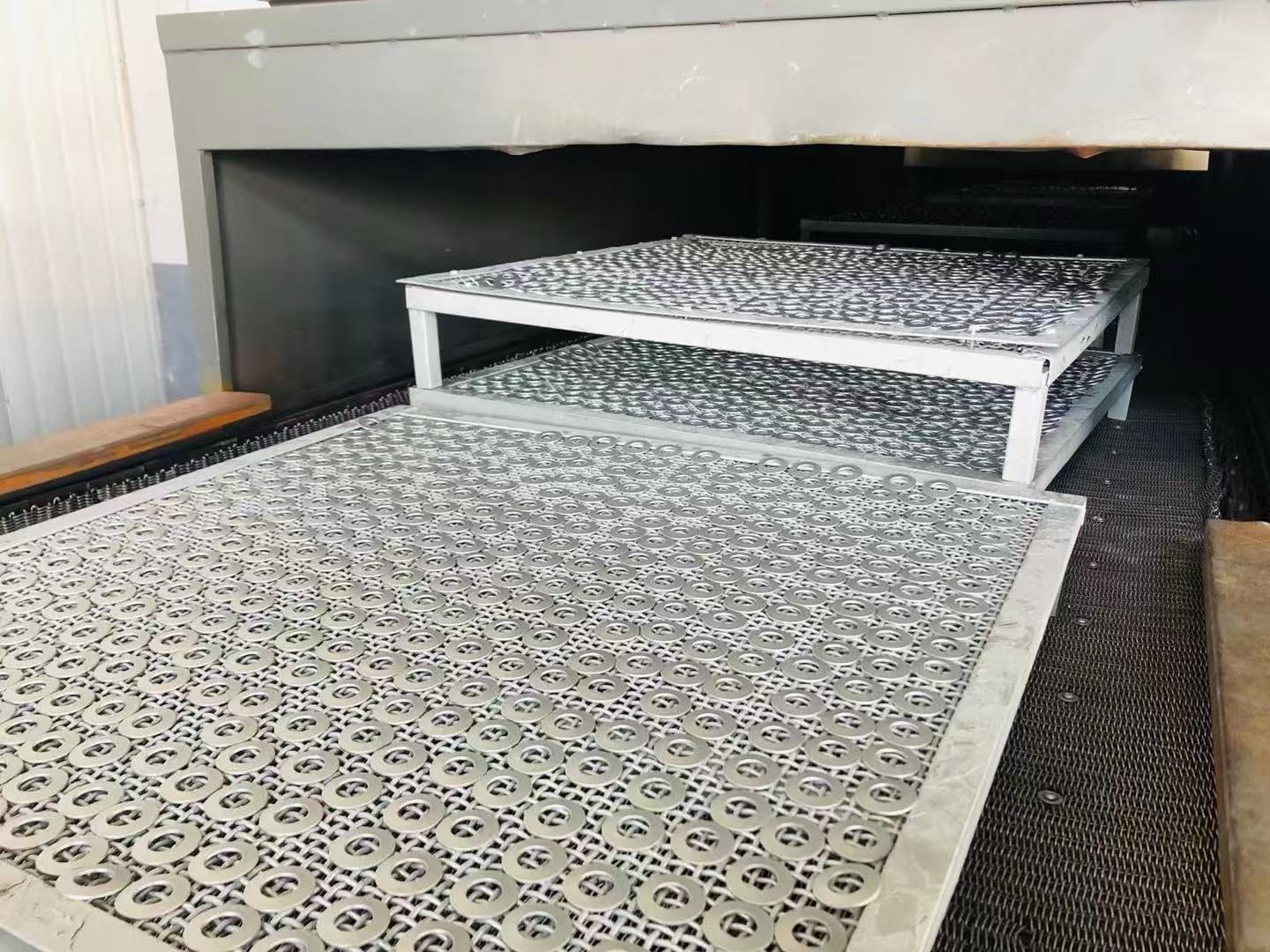
Which Surface Treatment Process Provides the Best Corrosion Resistance?
Among various surface treatment methods for springs, Dacromet coating offers the highest level of corrosion resistance.
Principle of Dacromet Coating
Dacromet is a new type of anti-corrosion coating primarily composed of zinc powder, aluminum powder, chromic acid, and deionized water. It is applied through a fully enclosed circulation coating and baking process, forming a thin protective layer on the spring surface. This unique film-forming process results in a coating with special structural and functional properties.
Corrosion Resistance
Dacromet coating provides superior rust protection, exceeding that of traditional electro-galvanization, hot-dip galvanization, or conventional coatings by 7-10 times. Testing has shown that springs treated with Dacromet can withstand salt spray tests for over 1200 hours without developing red rust. This exceptional resistance is due to the overlapping structure of zinc and aluminum flakes, which create a multi-layered barrier that effectively blocks corrosive agents from reaching the spring's base material, significantly delaying corrosion.
Additional Advantages
Apart from its outstanding corrosion resistance, Dacromet coating offers several other benefits:
- No Hydrogen Embrittlement: The process does not introduce hydrogen embrittlement, making it suitable for load-bearing components. This is particularly important for springs, which frequently endure stress and can suffer premature failure due to embrittlement in other coating methods.
- Strong Adhesion: The coating adheres well to the metal base and provides a solid foundation for additional coatings, making it easier to apply paint or other protective layers.
- High Penetrability: It can reach deep holes, narrow gaps, and other complex geometries, ensuring that all parts of the spring are effectively protected—an advantage over traditional electroplating, which struggles with complex shapes.
Comparison with Other Surface Treatment Methods
1. Black Oxide (Bluing)
Black oxide treatment creates a magnetite (Fe₃O₄) layer on the spring surface using an oxidizing solution such as sodium nitrite. This process provides some lubrication and is efficient, but its corrosion resistance is limited, typically protecting the spring for only about three months in air-exposed environments.
2. Phosphating
Phosphating involves immersing the spring in a solution containing manganese, iron, or zinc phosphates, forming a crystalline phosphate layer on the surface. While phosphating improves corrosion resistance 2-10 times compared to black oxide, it is still inferior to Dacromet. Additionally, phosphate coatings generally require subsequent painting or sealing for enhanced protection, and the process may introduce hydrogen embrittlement.
3. Electroplating
Electroplated coatings such as zinc, cadmium, copper, chrome, nickel, tin, and silver are commonly used for corrosion protection:
- Zinc plating provides basic corrosion resistance but is less effective than Dacromet.
- Cadmium plating is highly corrosion-resistant but is restricted due to cadmium's toxicity and scarcity.
- Chrome plating enhances surface hardness, wear resistance, and aesthetics, but its anti-corrosion properties are inferior to Dacromet in harsh environments.
4. Non-Metallic Coatings
Non-metallic coatings such as paints, asphalt, and plastic coatings can offer a thicker protective layer and good chemical stability, but they generally lack the long-term durability and adaptability to harsh conditions provided by Dacromet.
Conclusion
Among the common surface treatment methods for springs, Dacromet coating provides the best corrosion resistance. However, each surface treatment method has its own advantages and is suitable for different applications. When selecting a surface treatment process, factors such as operating environment, cost, and post-processing requirements should also be considered.
- Art
- Causes
- Crafts
- Dance
- Drinks
- Film
- Fitness
- Food
- Games
- Gardening
- Health
- Home
- Literature
- Music
- Networking
- Other
- Party
- Religion
- Shopping
- Sports
- Theater
- Wellness