How to Choose the Best Accurate Leak Detection
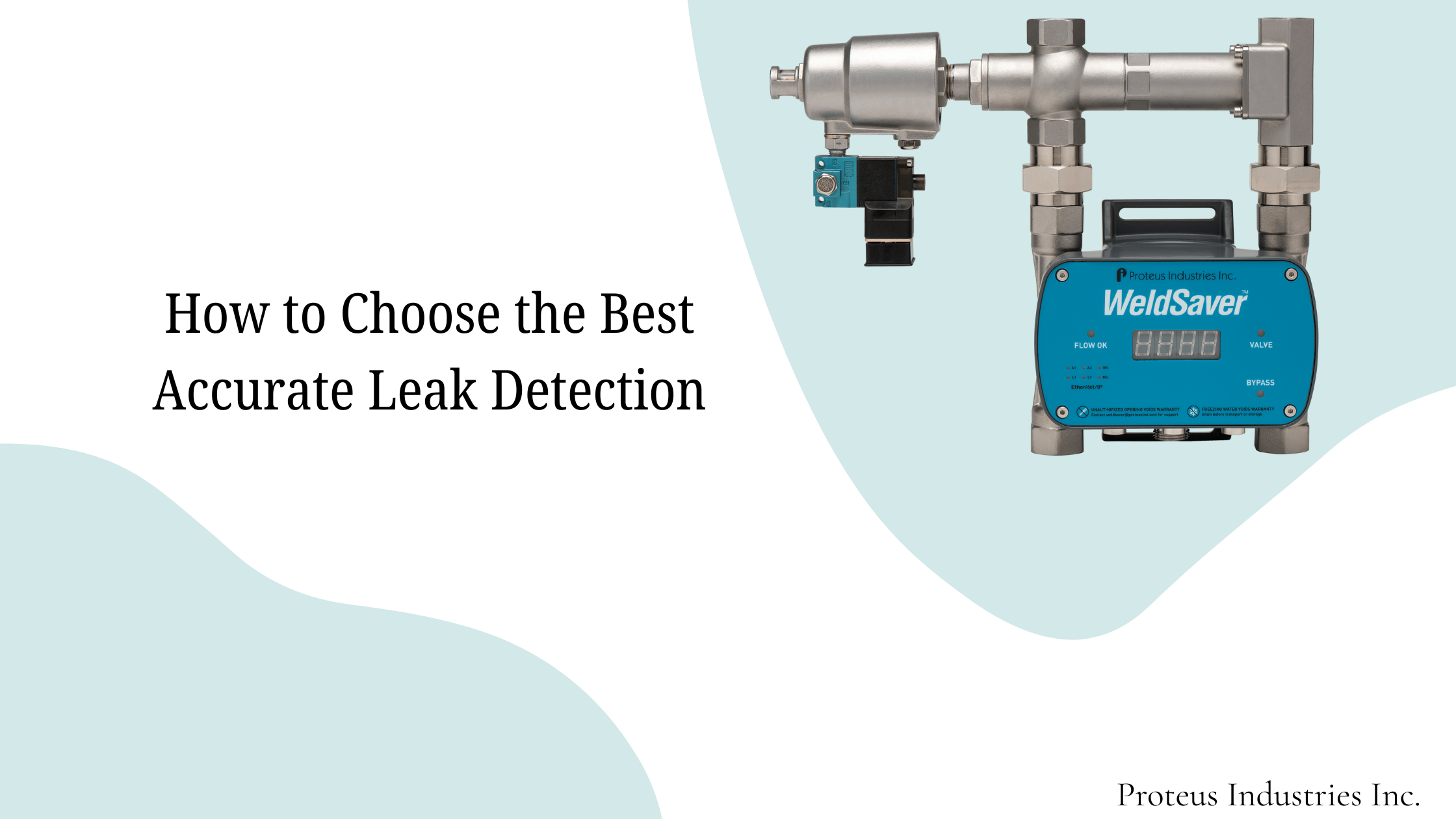
In industries where precision and safety are non-negotiable, the importance of accurate leak detection cannot be overstated. Whether it’s a manufacturing facility, a water treatment plant, or a high-performance welding operation, undetected leaks can lead to severe consequences, from costly equipment damage to production downtime and even serious safety hazards. That’s why investing in a reliable and efficient leak detection system is essential for maintaining seamless operations and safeguarding assets.
Accurate leak detection systems help monitor and identify leaks in real-time, ensuring swift corrective actions before minor issues escalate into major problems. These systems are vital in environments where fluids or gases are integral to production processes, like coolant flow in welding applications or pressurized pipelines. Businesses can improve operational efficiency, reduce maintenance costs, and enhance workplace safety by choosing the right leak detection solution.
However, selecting the most accurate leak detection system can be challenging, given the numerous technologies and products available. It requires careful consideration of detection sensitivity, response time, compatibility with existing equipment, and operational ease. In this guide, we’ll walk you through the key aspects to consider when choosing a leak detection system that fits your needs and ensures reliable, long-term performance.
Significance of Leak Detection in Welding
Leak detection in welding is critical for optimal efficiency, quality, and safety. A welding setup often relies on gas shielding, cooling water circulation, and controlled atmospheres to produce precise welds. Even the tiniest leak in these systems can lead to compromised weld integrity, increased defects, and material wastage. The failure to detect and rectify leaks can result in costly repairs, rework, and even safety hazards for workers. With the growing demand for high-precision welding, industries are adopting advanced leak detection methods to enhance performance and reliability.
Leaks in welding typically stem from various sources, such as hose cracks, loose fittings, and deteriorated seals. Traditional leak detection methods, such as visual inspections and soap bubble tests, often fail to identify micro-leaks that can significantly impact welding efficiency. This is where modern, technology-driven leak detection systems come into play, offering superior accuracy and reliability.
How Accurate Leak Detection Works
Accurate leak detection involves using advanced technology to identify leaks quickly, ensuring the welding process remains uninterrupted and efficient. One of the most effective systems for leak detection in welding is the WeldSaver technology developed by Proteus Industries. This system is specifically designed to detect leaks in cooling water circuits, a crucial aspect of ensuring the longevity and performance of welding equipment.
Modern leak detection solutions use various techniques, including ultrasonic sensors, pressure decay methods, and flow monitoring. These technologies allow manufacturers to pinpoint even the most minor leaks, preventing significant losses in productivity. Ultrasonic sensors detect sound waves generated by escaping gases or fluids, making them highly effective for identifying leaks not visible to the naked eye. Pressure decay methods involve monitoring pressure drops within a sealed system to identify potential leaks. Flow monitoring systems continuously track the fluid or gas movement rate, instantly flagging any irregularities that indicate a leak.
By implementing advanced leak detection systems, manufacturers can improve welding efficiency by minimizing downtime, reducing waste, and enhancing the overall quality of welded components. Furthermore, accurate leak detection ensures compliance with industry regulations, helping businesses avoid penalties and liabilities associated with defective welding operations.
Improving Welding Efficiency with Leak Detection Technology
A well-optimized welding process minimizes disruptions and maximizes output. Leak detection technology plays a significant role in ensuring seamless operations by preventing equipment malfunctions and inefficiencies. In water-cooled welding systems, detecting leaks in the cooling circuit is essential for preventing overheating and maintaining consistent weld quality. The WeldSaver system, for instance, continuously monitors coolant flow and provides immediate alerts when a leak is detected, allowing operators to take corrective action before a minor issue escalates into a significant problem.
Accurate leak detection enhances efficiency and improves workplace safety. Gas leaks, particularly in welding environments, can pose serious health risks to workers and increase the likelihood of fire hazards. By incorporating automated leak detection systems, industries can create a safer work environment while ensuring compliance with occupational safety standards. Additionally, reducing leaks translates to lower energy consumption and operational costs, making leak detection a cost-effective solution for welding businesses.
Integrating leak detection technology into welding operations also supports predictive maintenance strategies. Rather than waiting for equipment failure, manufacturers can proactively monitor system performance and address potential issues before they lead to costly downtimes. This proactive approach extends the lifespan of welding equipment and enhances overall productivity.
Choosing the Right Leak Detection System for Welding
Selecting the most suitable leak detection system depends on several factors, including the type of welding process, the materials used, and the specific challenges faced in the production environment. High-precision industries like aerospace and medical device manufacturing require highly sensitive leak detection systems to maintain strict quality standards.
Proteus Industries' WeldSaver system is a prime example of an advanced leak detection solution designed for welding applications. With its ability to monitor flow rates, detect leaks instantly, and prevent overheating, WeldSaver has become an industry standard for ensuring reliable welding operations. Other advanced leak detection technologies include helium leak detectors, thermal imaging cameras, and laser-based sensors, each offering unique advantages depending on the application.
Businesses looking to implement leak detection solutions should consider factors such as sensitivity, real-time monitoring capabilities, ease of integration, and maintenance requirements. Investing in a high-quality leak detection system ultimately improves welding efficiency, reduces defects, and enhances overall production outcomes.
The Future of Leak Detection in Welding
As technology evolves, leak detection systems become more sophisticated and efficient. Integrating artificial intelligence into leak detection technology is set to revolutionize the welding industry. Robust systems can analyze vast amounts of data in real-time, identifying patterns and predicting potential leaks before they occur. IoT-enabled sensors allow for remote monitoring and automated alerts, further enhancing the accuracy and responsiveness of leak detection processes.
Advancements in sensor technology and data analytics are also making leak detection systems more cost-effective and accessible to businesses of all sizes. With the rise of Industry 4.0, manufacturers are increasingly adopting innovative solutions to optimize their welding operations and achieve higher levels of efficiency. The future of welding will see greater integration of automated leak detection systems, reducing the need for manual inspections and minimizing the risk of production disruptions.
Finally
Accurate leak detection is critical to achieving maximum welding efficiency. Manufacturers can significantly reduce downtime, enhance product quality, and improve workplace safety by utilizing advanced technologies such as ultrasonic sensors, pressure monitoring, and AI-driven detection systems. Adopting innovative leak detection solutions, such as Proteus Industries' WeldSaver, ensures that welding processes remain efficient, cost-effective, and compliant with industry standards.
As welding technology advances, businesses must stay ahead by integrating the latest leak detection systems into their operations. Investing in accurate leak detection prevents costly defects and enhances overall productivity and sustainability. In an industry where precision and reliability are paramount, implementing cutting-edge leak detection technology is the key to achieving long-term success.
- Art
- Causes
- Crafts
- Dance
- Drinks
- Film
- Fitness
- Food
- Spellen
- Gardening
- Health
- Home
- Literature
- Music
- Networking
- Other
- Party
- Religion
- Shopping
- Sports
- Theater
- Wellness