The Top 5 Hull Corrosion Types and How to Protect Your Vessel
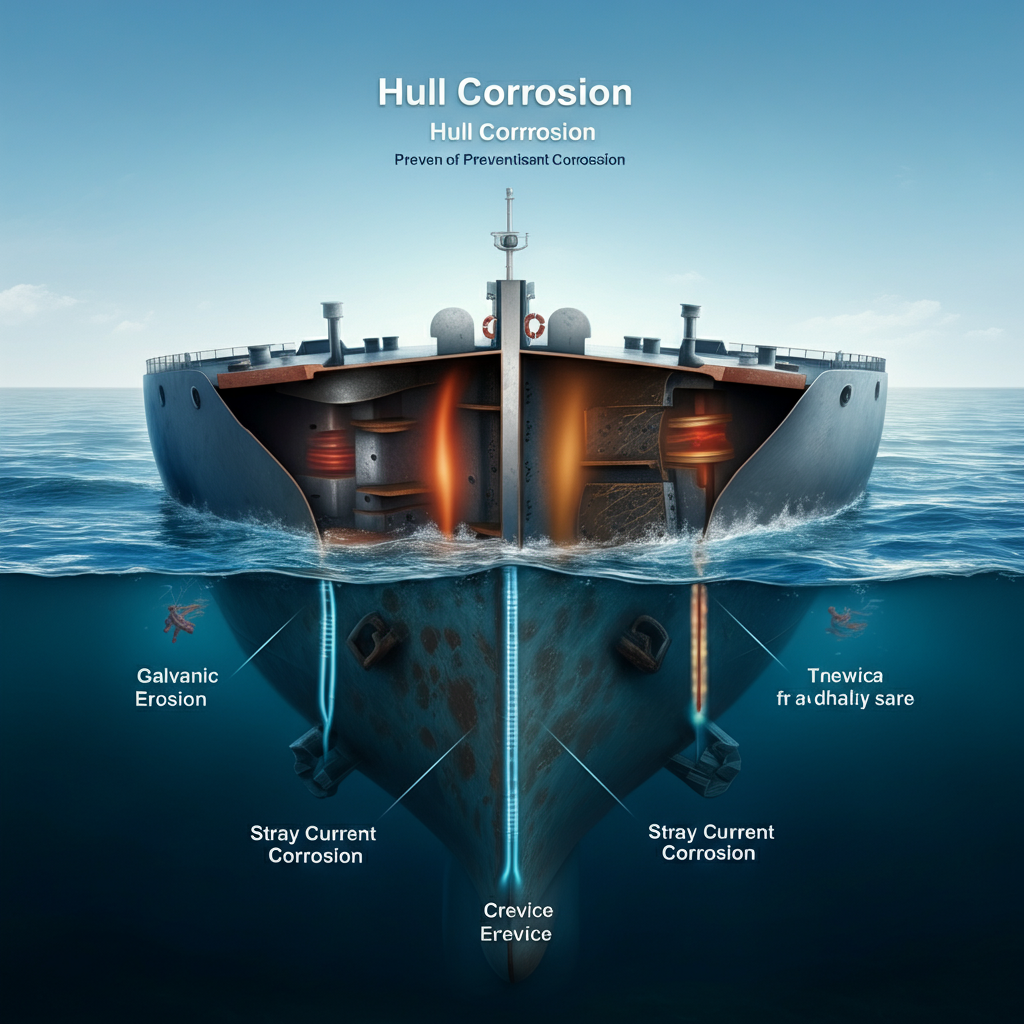
Hull corrosion is a challenge that has plagued ship owners, marine engineers, and boat enthusiasts for centuries. Left untreated, it can lead to devastating structural damage, costly repairs, and reduced vessel lifespans. Understanding the types of hull corrosion and the methods to prevent or mitigate them is crucial for anyone invested in maritime assets.
This comprehensive guide will walk you through the five main types of hull corrosion, explaining how they occur, their effects on ships, and actionable ways to protect your vessel.
What is Hull Corrosion?
At its core, hull corrosion refers to the gradual deterioration of a ship's hull material, typically caused by chemical or electrochemical reactions. These reactions often occur between the hull surface and its environment, whether water, oxygen, or other chemicals.
While most modern vessels are designed to withstand harsh marine environments, no material is completely corrosion-resistant. Steel, aluminium, and other alloys commonly used in shipbuilding are particularly vulnerable if proper precautions are not taken.
1. Galvanic Corrosion
What is it?
Galvanic corrosion happens when two dissimilar metals, such as Steel and aluminium, come into electrical contact while submerged in an electrolyte (like seawater). The less noble metal (anode) begins to corrode faster, while the more noble metal (cathode) is spared, forming a natural battery.
Why does it matter?
-
Galvanic corrosion is highly prevalent in marine settings because ships often utilise multiple metals in their construction (e.g., steel hulls combined with bronze propellers).
-
Left unchecked, galvanic corrosion can eat away at critical parts of the ship, including fasteners, fittings, and structural components, leading to loss of strength and possible leaks.
Preventative Measures:
-
Isolate Dissimilar Metals: Use insulating materials like rubber gaskets to separate metals.
-
Apply Protective Coatings: Ensure all metal interfaces are coated with high-quality, marine-grade paint or sealant.
-
Install Sacrificial Anodes: These are designed to corrode in place of the ship's more valuable components, thereby protecting your vessel. Common materials for anodes include zinc and aluminium.
2. Electrolytic Corrosion
What is it?
Electrolytic corrosion occurs when an external electrical current (often from onboard systems) passes through the water and strikes the hull. This accelerates the corrosion process. Unlike galvanic corrosion, which relies on the natural electrical potential between metals, electrolytic corrosion is triggered by artificial currents.
Signs of Electrolytic Corrosion:
-
Highly localised pitting or etching, especially around dissimilar metals.
-
Rapid degradation of sacrificial anodes despite proper placement.
How to Prevent It:
-
Inspect Electrical Systems: Ensure wiring is professionally installed and regularly inspected to avoid issues like leaking stray currents.
-
Cathodic Protection: Use an impressed current cathodic protection system (ICCP), which counters external currents by applying a controlled opposing current.
3. Erosion Corrosion
What is it?
Erosion corrosion arises when fast-moving water, often carrying abrasive particles like sand or debris, damages the protective coatings on a hull. Once the coating is breached, the exposed metal becomes highly susceptible to chemical reactions, leading to significant material loss.
Where Does it Occur?
-
Common areas include the bow, stern, propellers, and rudders, which frequently experience high-velocity water movement.
-
Internal systems such as piping and cooling systems are also susceptible.
Consequences of Erosion Corrosion:
-
It often leads to deep gouges and grooves, which compromise structural integrity.
-
Damage may spread internally, significantly raising repair costs.
Preventative Strategies:
-
Use Abrasion-Resistant Coatings: Apply durable coatings specifically designed for areas exposed to fast-flowing water or particle impact.
-
Regular Cleaning: Keep the hull free from biofouling, as marine life can increase drag and create abrasive conditions.
-
Design Improvements: Modify the vessel's hydrodynamic profile to minimise localised turbulence.
4. Crevice Corrosion
What is it?
Crevice corrosion occurs in narrow gaps or stagnant water regions where oxygen levels are depleted. At the same time, the surrounding areas of the hull remain oxygenated; these "dead zones" foster conditions for highly localised corrosion reactions.
Common Locations on a Ship:
-
Under gaskets or seals.
-
Near overlapping metal plates.
-
Inside threaded fasteners and around clogged joints.
Why is it Dangerous?
Crevice corrosion often progresses unnoticed because it's hidden beneath fittings or layers of material, making it difficult to spot during routine maintenance. By the time it's identified, significant damage may already be done.
How to Combat Crevice Corrosion:
-
Sealing Crevices: Use flexible sealants or silicone to fill gaps.
-
Frequent Inspections: Regularly assess areas prone to stagnation and ensure they're free from debris or blockages.
-
Improved Ventilation: Allow air to circulate parts prone to crevices, preventing stagnant moisture buildup.
5. Stray Current Corrosion
What is it?
Stray current corrosion is another severe type similar to electrolytic corrosion, but it's caused explicitly by uncontrolled electrical leaks from faulty equipment on the ship. Improper grounding or poorly insulated wiring can let electrical currents seep into the hull, leading to rapid material degradation.
What's at Risk?
-
Hull plating near electrical systems.
-
Components near pumps, motors, and jet engines.
Preventative Measures:
-
Routine Maintenance of Electrical Systems: Inspect regularly for signs of wear or damaged insulation.
-
Insulate Components: Use non-conductive materials where needed.
-
Proper Grounding: Ensure all electrical systems are adequately grounded to control current flow.
6. How to Prevent Hull Corrosion
Though understanding the types of hull corrosion is essential, prevention is ultimately your best defence. Here are general protective steps every ship or boat owner should take:
Regular Maintenance and Inspections
-
Hire professional marine engineers to perform thorough annual inspections.
-
Divers should routinely check for signs of cracks, pitting, and biofouling on submerged surfaces.
High-Quality Hull Coatings
-
Marine-grade paints and anti-corrosion coatings act as primary defences against environmental factors.
-
Opt for specialised coatings designed for high-salt environments.
Anode Replacement
-
Monitor sacrificial or impressed current anodes and replace them as soon as they begin to wear thin.
Monitor Electrical Systems
-
Equip your vessel with diagnostic tools to check for stray currents and ensure seamless grounding.
Keep the Hull Clean
-
Biofouling (algae, barnacles, etc.) increases drag, accelerates corrosion and creates erosion risks. Regular cleaning minimises these threats.
Protecting Your Ship for the Long Haul
Corrosion might be one of the biggest challenges in marine operations, but it is also one of the most manageable with proactive measures. By adopting state-of-the-art prevention techniques and staying informed, you can significantly extend the life of your vessel and save on expensive repairs.
If you're ready to protect your assets and secure peace of mind, start by assessing your ship for signs of the types of hull corrosion discussed in this blog. Implement anti-corrosion strategies today to safeguard your vessel tomorrow.
- Art
- Causes
- Crafts
- Dance
- Drinks
- Film
- Fitness
- Food
- Games
- Gardening
- Health
- Home
- Literature
- Music
- Networking
- Other
- Party
- Religion
- Shopping
- Sports
- Theater
- Wellness